加工の流れ
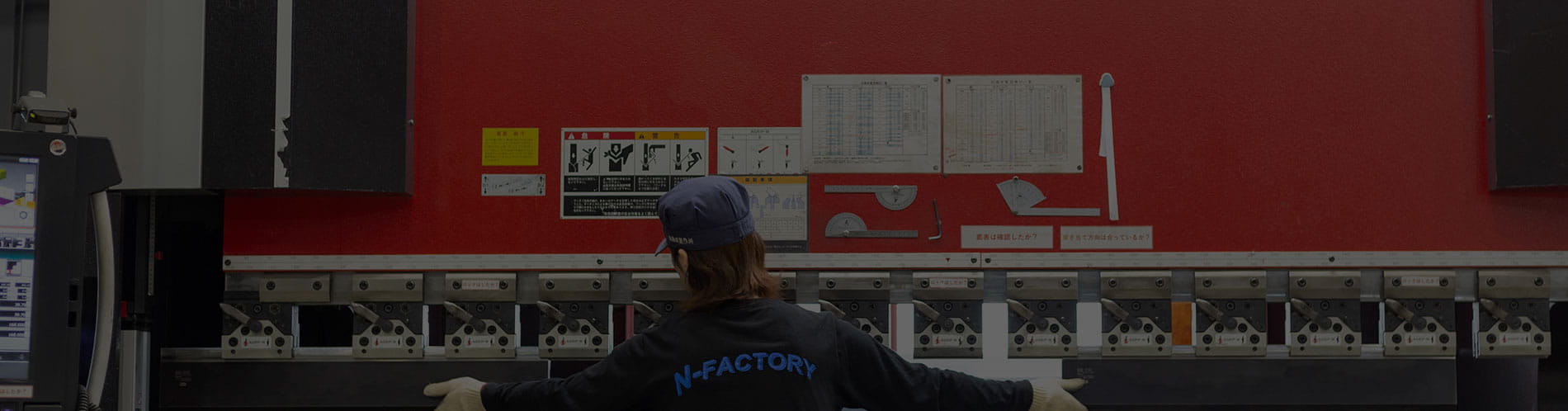
主な流れ
加工する製品や、精密板金加工、製缶加工、機械加工の加工種別によって手順は変わります。
各工程をクリックすると説明をご覧いただけます。
営業・見積もり提案
目的や用途に合わせ、最適な鋼材や形状で、可能な限り最短納品・最安値でご提案します。
お客様から預かった図面を、QCD(品質、コスト、納期)を第一に図面を読み取り製造側からより最適な提案をし、見積をさせていただいています。提案型の営業をさせていただいていることから、お客様の開発段階で会議に入ることも少なくありません。
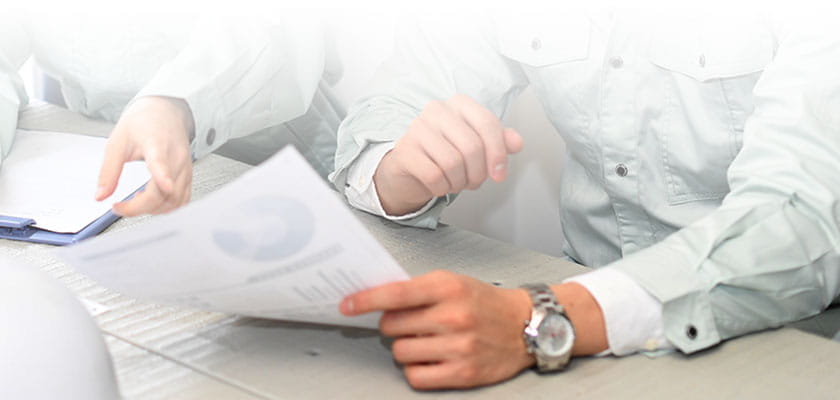
担当者の声
-
図面通りの見積ではなく、加工精度的に良い方法を提案し図面変更してもらうことも。
お客様から持ち込まれた図面 -
メーカーの設計の方が来られて、使用用途や製品の意図に合わせて製造側からの提案をします。
メーカーの企画会議に参加することも
受注
AIの自動入力で注文書を作成し受注を管理。
スケジュール別にタグ付けし現場へ回します。
営業から伝えられた受注内容を、AIを使って自動入力し注文書を作成します。お客様によって送られてくる形式は FAXやPDFと様々ですが、自動で読み取るための専用ソフトを使用して自動化しています。注文書は、スケジュール別に色分けしたタグをつけて、納期がひと目でわかるような状態で現場へ回します。
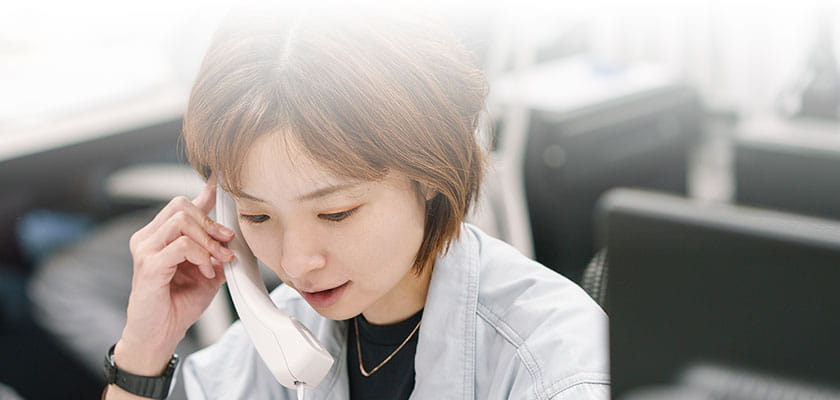
担当者の声
-
手打ちしていた注文書を、AIが自動入力してくれるので、その時間で他の作業ができるようになり効率アップしました。
注文書をAIで自動入力し効率アップ -
注文書はデータで図面は紙面にて管理。AIによる注文書は半永久に残り、図面は常に参照できるように整理棚で保管しています。
注文書や図面を管理する整理棚
CAD図面展開
レーザー加工機で加工する製品の図面を
専用のCAD室で作成します。
お客様からいただいた図面を理解して、レーザー加工するために頭の中で分解して平面の図面に描き換えます。サイコロを分解して6面体を作るイメージです。図面を見ながら、ある程度は頭の中で描きながら、ゼロからCADで描いていきます。できあがったプログラムはレーザー加工の担当者へ回します。
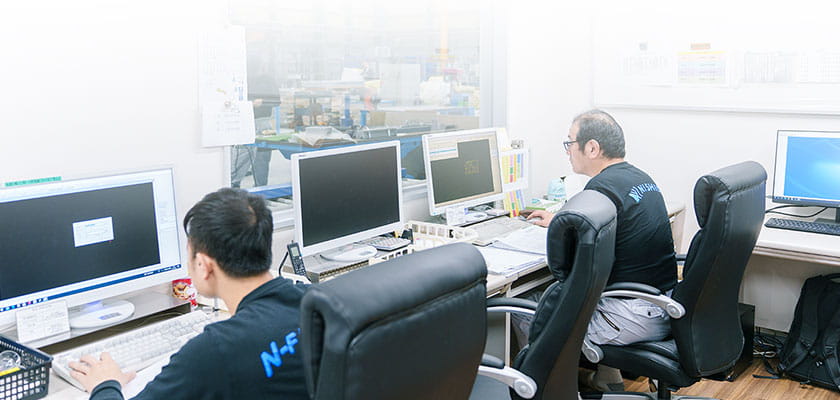
担当者の声
-
例えば、円錐形に部品を付ける場合、高さの円周を出して、さらに隙間を計算するので数学の知識が必要な時もあります。
数学の知識を使いながらCADを描くことも -
ある程度、自分の頭で考えながら、溶接や曲げのしやすさを考慮し、時々現場に確認しながら展開していきます。
加工のしやすさを考慮してCADを作成
五面CAD図面展開
五面加工機で削り加工する製品の図面を、専用のCAD室で作成します。
五面加工機で削り加工する製品の図面を、専用のCAD室で作成します。面と面とつなぎ立体の図面を描いていきます。図面は五面加工機に読み込まれ、図面に従って機械が加工を実行します。1/100㎜などの高い精度を実現する五面加工機の図面では、数値の間違いが大きなミスにつながるため、より慎重に作成が行われます。
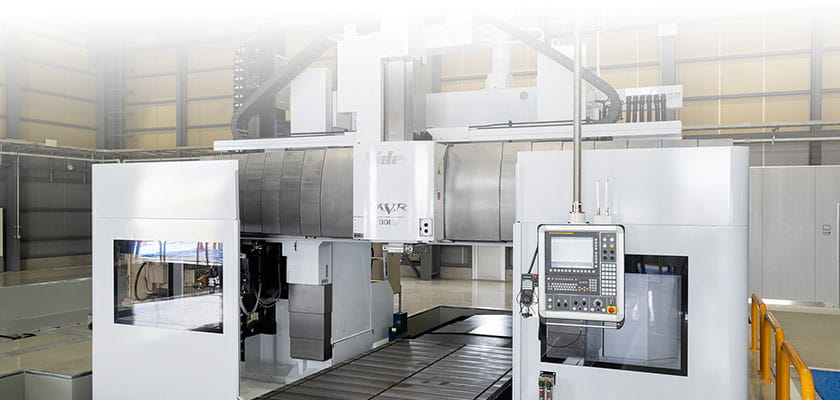
担当者の声
-
機械は指示した通りにしか動いてくれないので、1/100㎜などのどんなに小さな数字でも間違いがないよう確認します。
高い精度を求められるのでプログラムが重要 -
指示したデータの通りに機械が動くかもポイント。予期せぬ動きで機械や製品が傷つかないよう細心の注意を払っています。
プログラム通り機械が動くかをチェック
レーザー加工
レーザーを金属材料に照射。プログラムに従い穴あけ、切断、曲げラインなどを形成します。
各種鉄板を仕入れ、レーザーで穴あけ、切断、曲げラインなど抜き加工を行います。CADで組んでもらったデータを呼び出し、1枚の材料に無駄なく部品を当てはめてプログラムを組みます。工程の心臓部であるレーザー加工は段取りが全て。その後の工程がスムーズに進むよう、計画を立てながら進めていきます。
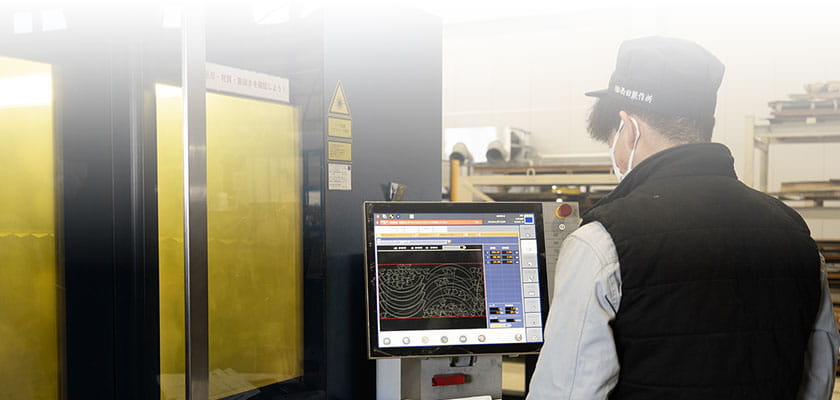
担当者の声
-
鉄なら30㎜、ステンレスなら16㎜程度までの厚さの抜きが可能。いかに無駄なく部品を埋められるかが大切です。
板の厚みごとに隙間なく部品を埋めていく -
加工後は熱くないですが、レーザーで抜いている瞬間とその部分は熱いので、板が溶けないように加工順を考え、プログラムを組みます。
板が溶けないよう熱伝導を計算しながら加工
五面加工(削り加工)
五面加工機で、主に1/10㎜〜1/100㎜など高い精度が求められる製品の削り加工を行います。
五面を一度に加工することが可能な五面加工機では、特に高い精度が求められる製品の削り加工を行います。半導体工場の製造ラインの筐体や、1/10㎜〜1/100㎜など厳しい公差が求められる製品の削り加工が可能です。正確なプログラミングはもちろん、機械のクセや動きを読んで、目で見て触りながら製品を仕上げていきます。

担当者の声
-
図面通り仕上げることは当然ですが、目で見て触って、削るギリギリの範囲でいかに美しく仕上げるかに挑戦しています。
目で見て触って面の美しさを確認 -
機械に乗らない大きな物でも、初めて使う難しい工具でも、ご要望があれば工夫してご希望の製品の完成を目指します。
機械より大きな製品の加工にもチャレンジ
仕上げ加工
バリ取り・ジョイント取り・穴加工などを施し、
安全性を高め次の工程への部品をまとめます。
レーザー加工や五面加工機の削り加工済みの部品の、バリ取り・ジョイント取り、穴加工、ネジ加工などの加工を行い、部品をまとめて次の工程へ引き継ぎます。お客様が怪我しないようにエッジを滑らかにし、取り扱いの安全性を高めています。
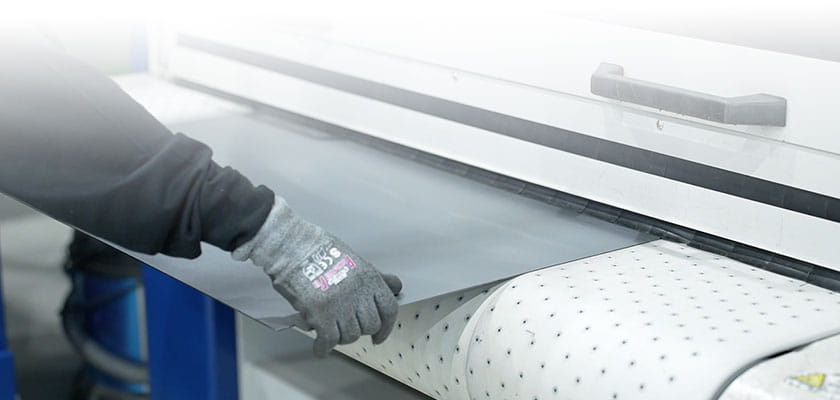
担当者の声
-
ボール盤による穴加工は斜めに開かないように注意し、大きいものや重いものは特にしっかり固定して作業します。
しっかり固定しボール盤でネジ加工を行う -
グラインダーで研磨する作業は、失敗が許されずとても緊張しますが、表面が綺麗になるのでやりがいがあります。
グラインダーで表面を研磨
曲げ加工
各種板材を90度や特定の形状に曲げます。職人の高い技術力で複雑な曲げも可能です。
各種板材を特定の形状に曲げます。基本的には鈍角、直角、鋭角で曲げますが、用途に合わせてアールをつけて筒状のものにすることもできます。円錐形などの複雑な形も、職人による高度な曲げの技術で、可能な限り加工を行い溶接のコストをカットし、美しい仕上げを実現します。
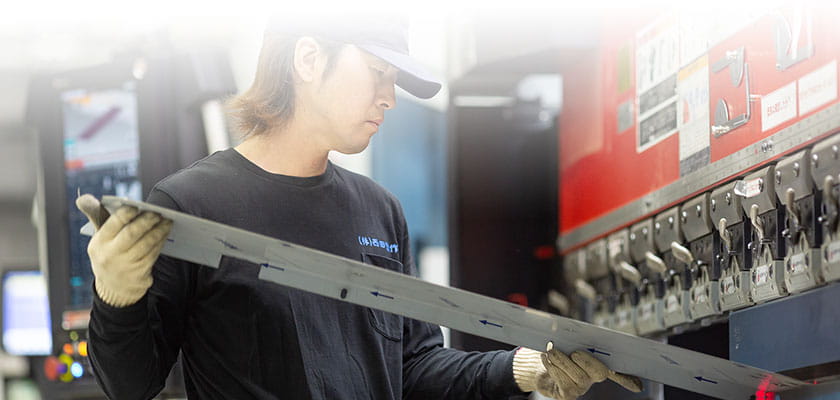
担当者の声
-
目で角度を確認しながら曲げたり、タイミングを見てペダルを踏んだりするため、職人の感覚が必要になります。
職人の感覚を駆使して曲げを調整 -
複雑な形の時は、他の面に当たらないよう緻密に計算し、その形に合った金型をセットします。
曲げる製品の形状に合わせて金型をセット
溶接仕上げ加工
TIG溶接と半自動溶接を使い分けながら、異なる材料に熱を加えて溶かし結合させます。
部品同士をつなげたり組み立てるため、TIG溶接や半自動溶接によって異なる材料を熱で溶かし結合させます。板厚や目的に応じて溶接機を使い分け、入熱量やスピードをコントロールしながら溶接します。強度が必要な結合部はより強固な溶接を、外面は美観を意識した溶接を施します。
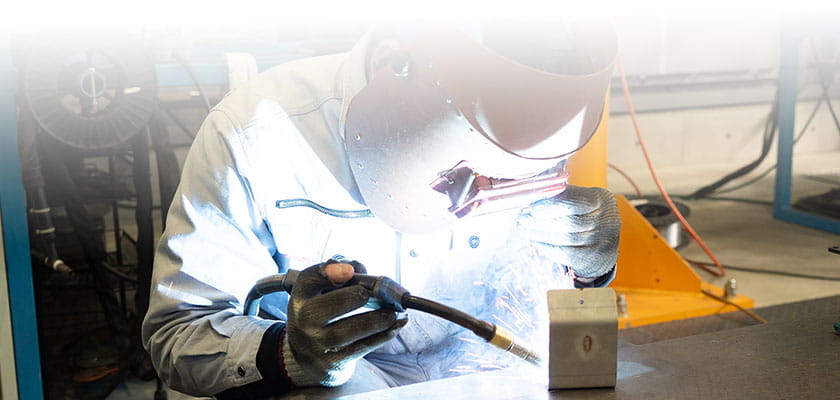
担当者の声
-
板厚や形状、用途によって溶接方法を変えます。ひずみが出ないよう、どのように強度を出すか考慮しながら溶接しています。
板厚や形状に合わせて溶接方法を工夫 -
外側の見える部分は、美観を意識して溶接します。職人の個性や熟練度が表われるのでやりがいがあります。
見える部分は美観を意識して溶接
ロボット溶接加工
ロボットアームと360°回転するターンテーブルで、高精度で複雑な溶接加工を繰り返します。
溶接の幅や位置、ロボットアームとターンテーブルの動きをプログラムで組み、自動で溶接加工を行います。人間の作業を最小限に抑えるとともに、作業の一貫性と品質が向上します。ロボットは人間のように疲れることがなく24時間稼働可能なため、主に製缶加工の大量生産に使用します。
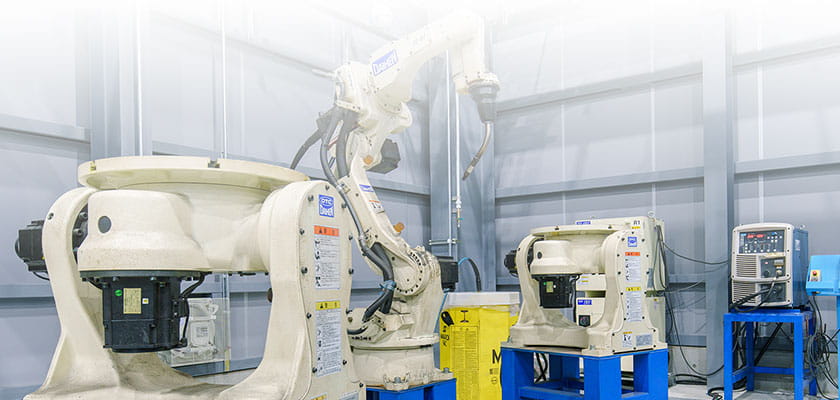
担当者の声
-
ロボットは溶接位置のズレがなく、溶接の幅も均等、所要時間も同じなので、大量に加工しても同じ品質で仕上がります。
同じ品質でスピーディに加工 -
プログラムを作るのに時間がかかるので、個数との兼ね合いで使用するかを判断。プログラムができれば誰でも操作できます。
プログラムができれば誰でも操作可能
- 関連設備
表面処理
溶接したステンレス製品の焼けを取り、美観を整えたり、腐食耐性を追加するための処理を行います。
溶接した製品の美観を整えたり、耐久性や腐食耐性などを追加するための処理を行います。ステンレスは溶接すると焼けが出ます。その溶接焼けを、化学反応を利用し電気分解によって綺麗にします。
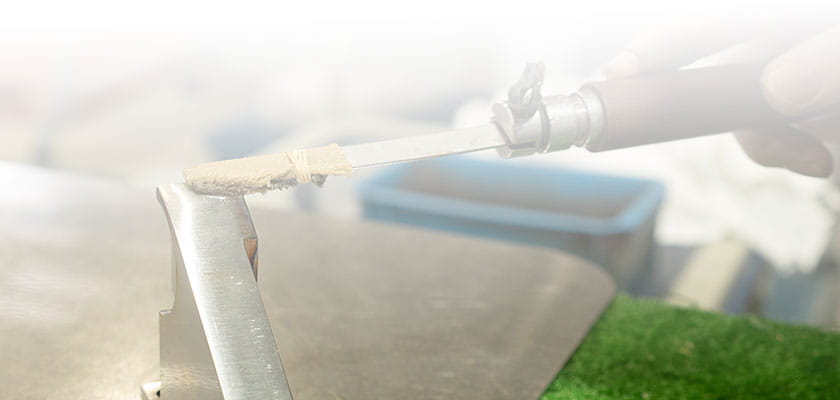
担当者の声
-
ステレンスについた溶接の焼けは、電解処理で取ります。溶接面が多い場合は、タンクに入れた酸につけて焼けを取ります。
ステンレスの焼け取り装置 -
電解処理が必要な複雑な部分は、液の溜まりを作って作業すると取れます。経験を重ねると早く処理できるようになります。
細かい技で溶接の焼けを取る表面処理
検査
製品が図面と適合しているか、外観・寸法・素材など様々な側面から検査します。
正しい素材が使用されいるかの検査、製品が図面通り品質基準や仕様と適合してるかを検査します。傷・へこみ・変形はないか、表面仕上げ・溶接・塗装の状態は問題ないかなど外観を検査。さらに、水平垂直・角度・厚さ・穴の位置などの寸法の検査などを行い、徹底的に製品をチェックします。
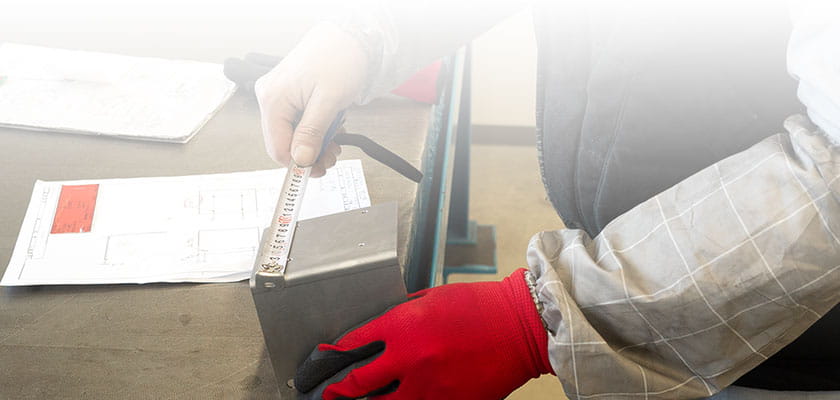
担当者の声
-
0.1㎜など細かい単位も全てしっかり測って確認します。0.01㎜や0.02㎜になるとマイクロ測定器を使うこともあります。
図面との誤差がないよう様々な測定器を使用 -
ネジ穴は、少しでも斜めになって途中で止まっていたりすると使えないため、見落とさないように検査しています。
ネジ穴のサイズ・位置・タップの有無を確認
出荷
完成した製品の表面を綺麗に洗浄し、ラップやエアーキャップで梱包します。
製品の最終チェックと梱包をします。汚れを専用の液で拭いて洗浄し、図面と見比べながら会社名や納期に間違いがないか確認します。鉄製品などは、外注先で塗装することもありますが、その場合も塗装が終わり次第こちらで再度確認してから出荷手配をします。最後に、製品をラップやエアーキャップで梱包します。
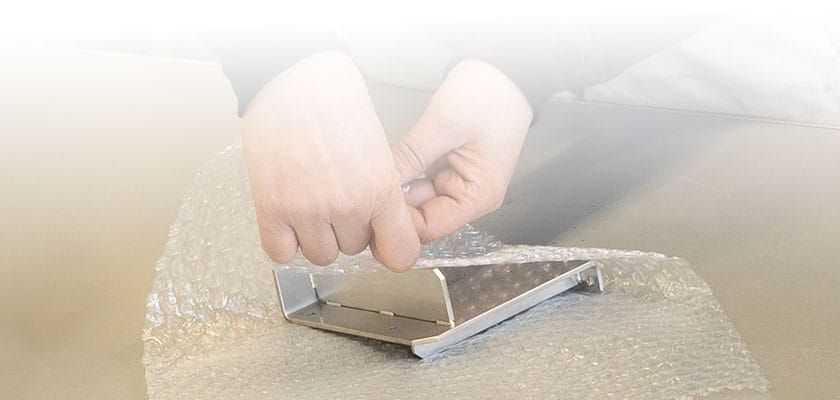
担当者の声
-
様々な工程の間に、製品に付いてしまった埃や汚れを、シンナーなどの液体で表面を綺麗に拭いて洗浄しています。
シンナーなどの液体で表面を洗浄 -
輸送中の傷や汚れを防ぐために、一つひとつ丁寧に梱包します。完成時の品質のまま安全に届けるための大切な作業です。
できあがった製品に傷がつかないよう梱包
配送・納品
製品に適切な梱包を行い、自社トラックまたは配送業者を使い、納期までに配送します。
作られた製品を搬送中に動いたり、崩れたりしないように積み込みし、大切な製品をお届けします。
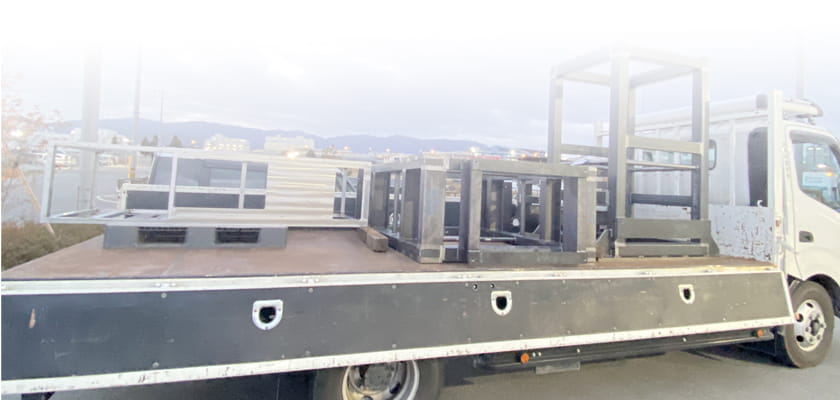
担当者の声
-
3.5t、4t、他3台の車を所有しています。部品に合わせ、車を使い分けて配送します。
所有する3.5t、4t、他3台の車で配送 -
自社トラックで運べない大きさのものは、協力先の配送業者にお願いして納品します。
協力先の10tトラックで配送